3D-gedruckte Teile erobern immer mehr unsere Welt. Ein gutes Beispiel dafür ist der folgende Anwendungsfall, bei dem die Fähigkeit der additiven Fertigung, beliebige Strukturen, beispielsweise Gitter, auch Lattice genannt, zu erstellen, die Hauptrolle spielt. Die Kunststofftechnikspezialisten von Oechsler in Ansbach/Mittelfranken, setzen auf die 3D-Drucktechnologie von Carbon, um in die additive Serienproduktion von Rückenpolstern für Rucksäcke von Jack Wolfskin einzusteigen.
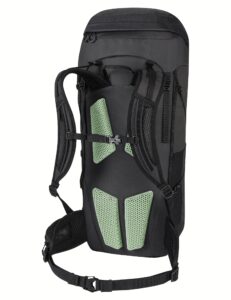
Das neue Modell „3D Aerorise 40“ sowie die gesamte „Aerorise“-Rucksackserie von Jack Wolfskin sind mit vier innovativen Rückenpads ausgestattet, die von Oechsler mit der 3D-Drucktechnologie von Carbon hergestellt werden. Die Pads sind für die angrenzenden Körperzonen optimiert und setzen neue Maßstäbe in Ergonomie und Tragekomfort bei gleichzeitiger Gewichtsreduktion.
Die Rückenpads bestehen aus einer offenen Gitterstruktur, die nur im 3D-Druckverfahren hergestellt werden kann. Platziert werden sie im Schulter- und Lendenwirbelbereich und ersetzen traditionelle Polsterungen aus Schaumstoff. Das Gitternetz besteht aus tausenden stabförmigen, elastischen Verbindungen unterschiedlicher vertikaler und horizontaler Festigkeit. So können die Härtegrade im Bauteil an die Körperstruktur angepasst werden: Weich, wo Komfort entscheidend ist, und fester, wo Stabilität gefragt ist.
Zudem bietet die Gitterstruktur zahlreiche Vorteile, die mit herkömmlichen Produktionsverfahren bislang nicht erreicht werden können. So ermöglicht sie eine Gewichtsreduzierung, verbessert die Belüftung und führt so zu einer Temperaturreduzierung in Belastungszonen um bis zu fünf Grad Celsius. Ein weiterer Vorteil ist ein erhöhter Tragekomfort – insbesondere bei hoher Belastung.
Carbon: Serienfertigung von Rückenpolstern im 3D-Drucker
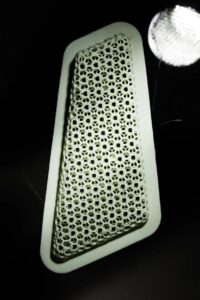
Matthias Weißkopf, General Manager von Oechsler Motion und Senior Vice President Global Product & Technology Development, sagt: „Wir freuen uns, dass wir Jack Wolfskin bei der Entwicklung der Rucksackserie ‚Aerorise‘ unterstützen durften. Mit unserem Know-how in der additiven Fertigung ist es uns gemeinsam gelungen, die Produkteigenschaften des Rucksacks zum Nutzen der Kunden zu verbessern. Die additive Fertigung wird die Gestaltungs- und Produktentwicklung von Outdoor-Ausrüstung und Sportartikeln in den kommenden Jahren maßgeblich verändern. Wir sehen in diesen Bereichen erhebliches Wachstumspotenzial für die Entwicklung und Serienfertigung im 3D-Druck.“
Andreas Tulaj, Vice President Sales Europa bei Carbon, ergänzt: „Die integrierten Endverbraucher-Materialien, die Software und die 3D-Drucker von Carbon ermöglichen es, die Markteinführung von Produkten in großem Maßstab zu beschleunigen – von der Idee bis zur Produktion. Mithilfe der ‚Idea-to-Production‘-Plattform von Carbon hat Jack Wolfskin die Leistung des Rucksacks ‚3D Aerorise 40‘ verbessert und in Zusammenarbeit mit Oechsler Komponenten entwickelt, die mit herkömmlichen Fertigungsmethoden nicht so schnell entwickelt und auf den Markt gebracht worden wären. Wenn sich bekannte Marken wie Jack Wolfskin dem 3D-Druck zuwenden, ist das ein starkes Zeichen dafür, dass die additive Fertigung weiterhin Innovationen ermöglicht.“
Magdalen Hamel, Category Manager Equipment bei Jack Wolfskin, fügt hinzu: „Komfort, Lastenkontrolle und Belüftung sind langjährige Herausforderungen im Rucksackdesign. Die in unseren Aerorise-Rucksäcken vorgestellte Technologie ist erst seit kurzem verfügbar und wegweisend für die Branche. Das Design ist aus technischer Sicht wirklich beeindruckend und bestärkt uns in unserer Überzeugung, dass wir gemeinsam mit unseren Partnern einen bemerkenswerten Unterschied machen und die Branche einen Schritt nach vorne bringen können.“
Erfolgreiche Umsetzung additiver Großserienproduktion bei Oechsler
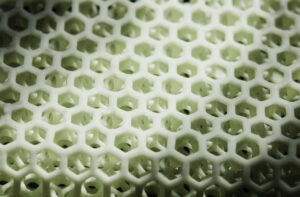
Der Drucker von Carbon arbeitet nach dem DLS-Druckverfahren, das mit Kunstharz arbeitet. Entscheidend für die Effizienz der Serienfertigung ist darüber hinaus die Expertise von Oechsler in der Vor- und Nachbearbeitung von Produkten. Nachbearbeitungsschritte wie die Hitzebehandlung geben den im 3D-Druck hergestellten Komponenten erst ihre definierten mechanischen Eigenschaften.
Additive Manufacturing ist eine der am schnellsten wachsenden Fertigungstechnologien, die dank ihrer Flexibilität bereits in vielen Industrien überzeugt hat. Im Bereich Sportartikel haben Oechsler und Carbon bereits zahlreiche Projekte wie die Serienproduktion von Fahrradsätteln oder Dämpfungselementen für American-Football-Helme umgesetzt. Die erfolgreiche Entwicklung und additive Serienfertigung der Rückenpads für Jack Wolfskin am Standort Brodswinden ist ein weiteres Kapitel der gemeinsamen Erfolgsgeschichte von Carbon und Oechsler seit Beginn ihrer Partnerschaft im Jahr 2016.
Ich finde es immer interessant, reale Anwendungen für 3D-Druckbauteile zu sehen und bin begeistert, das diese Bauteile an einer so exponierten und belasteten Stelle bestehen können und zudem Bauteile aus herkömmliche Fertigung schlagen.